Open Cut
Operations Planning & Execution Software
Optimise Open Cut Mining Operations with Our Integrated Digital Platform
In the dynamic environment of open-cut mining operations, maintaining operational efficiency while managing complex scheduling, resource allocation, and enabling activities is crucial for meeting production targets and ensuring safety. Many operations still rely on disconnected systems and manual processes, leading to inefficient resource utilisation, poor coordination between departments, and challenges in managing enabling activities. This article explores the key challenges in open-cut mining operations and introduces our software solution designed to integrate planning, execution, and resource management across all operational areas.
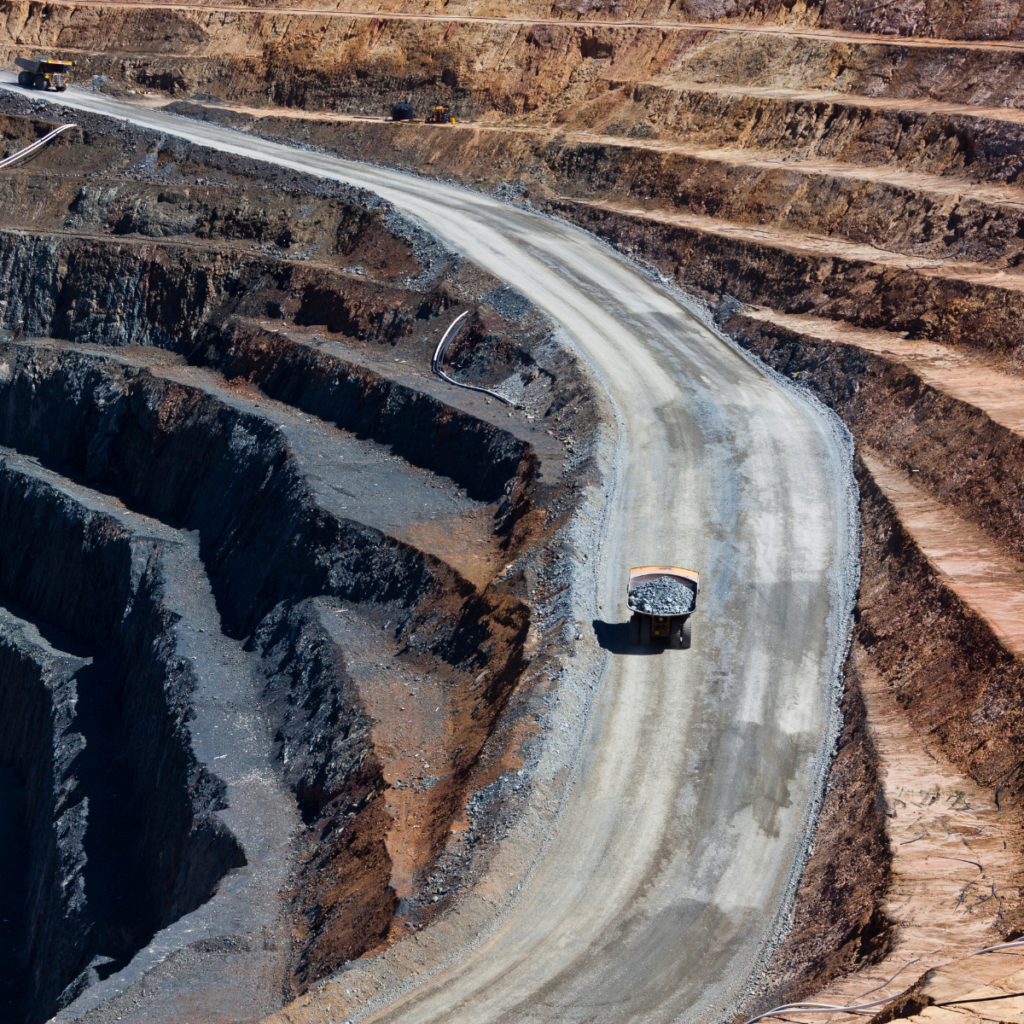
Challenges
Enabling Activities Integration
One of the most pressing challenges in open-cut mining operations is the fragmented approach to planning and executing enabling activities. Critical enabling tasks are typically managed in isolation by design engineers, technical services, and mine scheduling teams, creating dangerous gaps in operational coordination. This siloed approach means pump strategies are often neglected until they become urgent constraints, while dragline plans are developed without considering their mine-wide impact. The situation is further complicated by the tendency to treat operational continuity enablers as discrete projects rather than integral components of the continuous work schedule. As a result, essential tasks are frequently deprioritised until the last possible moment, leading to high levels of conflict and reactive problem-solving in the field. The implications of this disconnected approach are severe: production delays become commonplace, area access is compromised, and resource costs escalate unnecessarily. Moreover, the impact on equipment effectiveness is significant, with machine priority and availability issues directly affecting production cycle times, maintenance strategies, and ultimately, site safety.
Planning and Execution Alignment
The disconnect between mine planning and operational execution represents another critical challenge in open-cut operations. Current practices heavily rely on spreadsheets and manual tools for integrated work management, creating a dangerous gulf between planned activities and actual execution. Teams often work in isolation, unaware of how their tasks impact or depend on others, leading to confusion, delays, and duplicated efforts. Real-time communication suffers without a unified platform to track and share information, and the ability to address emerging issues is severely compromised. This misalignment has far-reaching implications: project completion is delayed, bottlenecks become more frequent, and the risk of errors increases significantly. Critical tasks are often overlooked or deprioritised, disrupting workflow and reducing overall productivity. In the long term, this lack of coordination makes it increasingly difficult to meet operational goals, consistently miss deadlines, and ultimately hinders the operationās ability to execute strategic initiatives efficiently.
Resource Optimisation
Resource management presents a significant challenge in open-cut mining operations, particularly regarding labour hours and equipment utilisation. Without clear visibility into available resources, operations struggle to effectively schedule tasks within each shift, leading to either over-scheduling or under-utilisation of valuable assets and personnel. This uncertainty creates a ripple effect across the operation, impacting budget compliance, contractor spending, and overall labour costs. The lack of effective resource planning frequently results in task delays and bottlenecks, as resources are not properly allocated to meet operational demands. Workers often find themselves either overburdened or underutilised, leading to decreased morale, increased fatigue, and potential safety risks. The financial implications are severe: labour budgets are exceeded, operating costs per ton increase, and opportunities for strategic investments in equipment and infrastructure are lost. Moreover, when safety is compromised due to rushed or inadequately staffed jobs, the operation faces potential incidents and increased workforce turnover.
Operational Waste Management
A significant but often overlooked challenge in open-cut mining is the accumulation of operational waste through both scheduled and unscheduled delays. Operations frequently face extended wait times for blast charge access and delayed drill operations due to poor coordination of mine services. These delays are often exacerbated by inefficient pre-strip activities in constrained areas and unnecessary dozer rework. The impact of these inefficiencies creates a cascading effect across various operational setups, from drill and blast to mine production and milling operations. The implications of this operational waste are substantial: production cycles extend beyond planned timeframes, operational costs increase significantly, and overall productivity suffers. This continuous cycle of delays and rework places additional strain on already limited resources and makes it increasingly difficult for operations to meet production targets while maintaining cost-effective operations.
Solution
Integrated Operations Planning & Execution
Our software suite provides a unified, digital approach to managing open-cut mining operations from the 90-day plan down to the shift level. Instead of relying on fragmented tools like spreadsheets and whiteboards, our platform creates a connected environment where planning, execution, and adjustments are centralised in one place. By digitising shift plans and linking tasks with specific equipment, locations, and personnel, our software ensures teams have clear visibility into what needs to be done and when. This clarity reduces miscommunication and keeps operational tasks aligned with production goals.
Our platform enables mine planners, schedulers, and superintendents to adjust plans dynamically based on actual conditions in the field. Unlike traditional manual systems, where updates are slow or non-existent, our software incorporates real-time data from the pit into the plan throughout the shift. This dynamic updating ensures that enabling activities, production, and maintenance teams are coordinated, leading to fewer delays and improved efficiency.
Dynamic Resource Management
Our software provides an integrated view of human resources and equipment, allowing supervisors, planners, and schedulers to dynamically allocate these resources across tasks and locations based on current needs. In open-cut mining, delays in haul truck cycles, shovel utilisation, or pre-strip activities can lead to significant production losses. Our platform enables supervisors to reassign resources quickly, ensuring that critical tasks are completed on schedule.
Instead of waiting for weekly reviews or end-of-shift reports, teams can make data-driven decisions during the shift, tracking equipment performance, task completion, and resource availability in real-time. This ensures that resources like dozers, loaders, and haul trucks are utilised efficiently, reducing downtime, and boosting productivity.
Real-Time Data Utilisation and Adaptive Execution
The ability to adapt to changing conditions is essential in open cut mining. Our software supports this by serving as a central data repository for task progress, equipment performance, and operational updates. As tasks are executed, supervisors and planners log progress and deviations in the system, providing the most current information to the team.
This real-time data allows schedulers and supervisors to adapt shift plans based on actual performance, optimising production and reducing delays. For example, if a critical enabling activity, like drainage preparation, is delayed, planners can use real-time insights to shift resources and prioritise downstream tasks. This adaptive approach ensures seamless alignment between planning and execution, minimising the impact of unforeseen challenges.
Enhanced Safety and Compliance
Safety and compliance are embedded directly into our platform. Features like safety checklists, skills tracking, and compliance reporting enable supervisors to ensure that tasks are performed by personnel with the appropriate certifications and experience. Supervisors can monitor equipment conditions and ensure maintenance is prioritised, reducing risks and maintaining operational continuity.
For example, if a haul truck is flagged for maintenance, it can be taken offline and replaced with an available resource, ensuring that safety is not compromised. These safety protocols are seamlessly integrated into the planning and execution process, providing teams with the tools to monitor and manage risks effectively.
Cross-Functional Collaboration
Our software fosters collaboration across planning, scheduling, and operational teams by providing real-time communication and shared visibility into tasks and progress. This cross-functional integration ensures that everyone, from planners to shift supervisors, operates with the same up-to-date information, reducing conflicts and improving overall efficiency.
With multi-user capabilities and intuitive dashboards, our platform breaks down silos, enabling teams to work together effectively. This culture of collaboration enhances coordination, minimises errors, and drives better outcomes.
Continuous Improvement & Feedback Cycles
Our software plays a critical role in driving continuous improvement across open-cut mining operations. By capturing detailed shift data, including task completion, equipment utilisation, and production metrics, the platform empowers mine planners, schedulers, and BI leads to analyse trends and identify areas for improvement.
For instance, if delays in blast charge setup are repeatedly causing bottlenecks, the data can pinpoint specific issues, allowing the team to optimise scheduling and resource allocation. This iterative feedback loop refines week-to-shift planning processes, ensuring that future plans are more accurate and aligned with actual performance.